Employment Experience
The Chemours Company Co-Op
Manufacturing Engineer
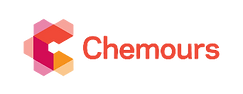
After my time at SpaceX, I sought to pursue my interest in manufacturing processes. This led me to join the Chemours Company in a Co-Op position working full time while completing the final semester of my master's degree. As a manufacturing engineer during the spring of 2024, I immersed myself in projects concerning intricate high-pressure vessels housing hazardous materials, refining my skills in designing and manipulating pipes and tubes on-site.
My role increased my understanding of various equipment, including pumps, compressors, mechanical seals, regulators, and autoclaves, and addressing complex challenges stemming from component failures. Utilizing Python, I optimized the inventory of flex hoses and improved their documentation. Additionally, frequently read and worked with Part and Instrumentation Diagrams (P&IDs) as well as collaborated with mechanics and operators, to troubleshoot site issues. My work also delved into environmental compliance and hazardous material management, where I learned about risk mitigation strategies and the unique complications that arise when working with unique compounds. One noteworthy project involved designing and implementing a nitrogen sweep system into a pump handling sub zero (-13°F) process materials to prevent corrosion-induced pump failures, showcasing my adeptness in engineering solutions to problems.

This role was a little out of my comfort zone, but i was frequently pushed to learn more about chemistry and concepts that were new to me and I was thankful for it! Some of the chemistry concepts I learned about were azeotropes, homolog distributions, phase cuts, and liquid-vapor separation to name a few.
Problem
The pump was taking in air and the colder body of the pump would allow for condensation in the hydraulic reservoir of the pump. Over time the condensation was causing corrosion and ultimately pump failure

Solution

To prevent this condensation from happening, I designed a nitrogen sweep system that would constantly run N2 through the reservoir. This would keep the chamber free of air so no moisture would be available to condense.
Space Exploration Technologies (SpaceX) Internship
Associate Engineer - Supply Chain Engineering
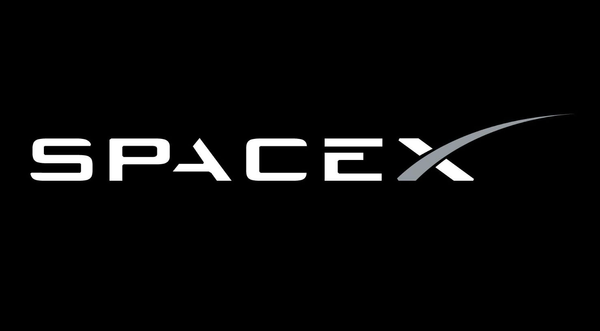
In the summer of 2023 I had the incredible opportunity of working at SpaceX headquarters in Hawthorne, CA on their supply chain engineering team. The projects I worked on during my time at SpaceX had direct impacts on the company in a way that made me proud of the work myself and the team I had work with had accomplished. I can't dive into the specifics of the work that I performed for the company, but my projects gave me hands on experience working on composite manufacturing and process improvement. Additionally I learned first-hand about the Aerospace supply chain, interacting with vendors, industry standard fittings and tubing assemblies, resolving supplier deviation requests, and how to contribute in a fast paced and high pressure work environment. My experience at the company was invaluable and will serve as a stepping stone for my future endeavors as an engineer!

Undergraduate Research at UD Center for Composite Materials
X-ray Computed Tomography of Impacted Composites
I have been performing research at the University of Delaware's Center for Composite Materials under Dr. Bazle Haque (bzhaque@udel.edu) studying impact dynamics of composites using both experimental and computational modeling techniques. I also developed a website for our research group which you can view here! Recently I have been investigating the interior damage of composite specimens using X-ray computed tomography (CT) after we impact them experimentally on Instron machines. The scans give the group the insight on the specific damage mechanisms that occur during testing without cutting the sample physically and damaging the interior failure architecture as a result. In addition to X-Ray CT, I frequently design testing fixtures to attach to an Instron machine using Solidworks. Find more info about the Center for Composite Materials here.

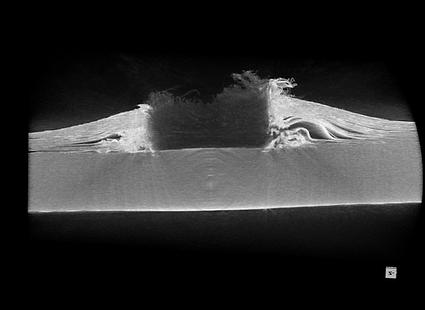
